定期メンテナンスで生産ラインの停止を解消
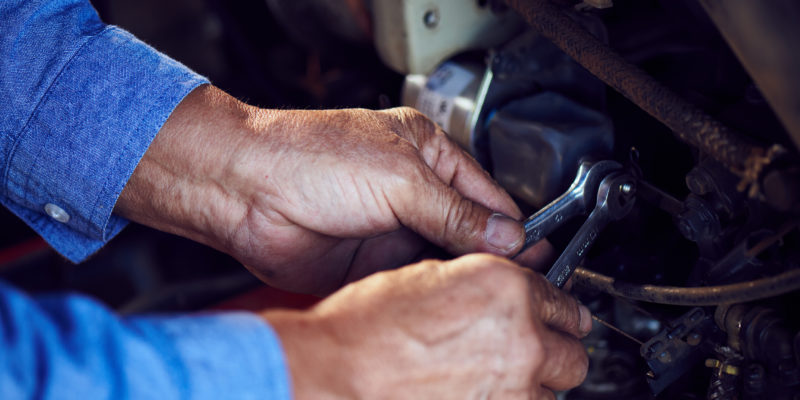
押出機モーターのベアリング不具合による生産ラインの停止が頻繁に起きていました。
主なメンテナンス内容はベアリングの交換、コイルの捲替、その他部品の確認・交換でした。
全台のメンテナンスを実施したため、その後は各モーターを5年に1度定期メンテナンスすることで、生産ラインの停止がなくなりました。
当サイトをご覧になられた栃木県の化学メーカーのお客様からのご相談でした。
お問い合わせ内容は押出機モーターのベアリング不具合による生産ラインの停止が頻繁に起きているということでした。
工場内にモーターは全20台設置してあり、「モーター故障→生産ライン停止→メンテナンス」の対応が繰り返し頻繁に発生している状態でした。当初、モーター故障時に都度対応という形で進めていたのですが、あまりにも非効率的だったため、一度全台のメンテナンスをし、その後定期的にメンテナンスをする提案をしました。
お客様に提案の了承をいただき、工場内全20台のモーターをメンテナンスしました。
主なメンテナンス内容はベアリングの交換、コイルの捲替、その他部品の確認・交換でした。
全台のメンテナンスを実施したため、その後は各モーターを5年に1度定期メンテナンスすることで、生産ラインの停止がなくなりました。
定期メンテナンスで生産ラインの停止はなくなったものの、お客様はコスト面について懸念されていました。
昭和電機の定期メンテナンスは故障時に対応するより安く済むため、その旨を説明し、納得いただきました。
具体的に、モーター故障時のメンテナンス費用は200~300万円、5年に1度の定期メンテナンス費用は60~90万円です。さらに故障時の対応は生産ラインの停止も余儀なくされるため、実質の費用はもっとかかりますといった内容です。
実際に生産ラインの停止にお悩みのお客様だったため、定期メンテナンスの重要性についてはご理解いただき、定期メンテナンスをご依頼いただいております。
お客様に定期メンテナンスの重要性をご理解いただいたことで、今後も定期メンテナンスにより、お客様の設備の安定稼働に貢献していきたいと思います。
導入事例をもっと詳しく知りたい方へ